3d Print Hexagon Lattice Design Fusion 360
2 Comments
3D printing allows for users to create some very intricate forms quite easily. By tinkering the internal geometries of printed parts they can achieve some pretty impressive mechanical properties. One of the best ways to achieve good strength-to-weight ratios, desirable shock and sound absorption and larger surface areas is to print objects with lattice structures.
Why Lattices?
What makes lattices unique is how they lay out materials into design elements to form an ideal structure that comprise of micro-architectures with a network of nodes and beams or struts. This format dramatically reduces weight while retaining structural integrity and giving a larger degree of control over certain characteristics. These interlinking portions can enhance various areas of performance and even use up less material without weakening the object or compromising its integrity.
Lattices have always been present in nature, from the internal structure of bones to metal crystallography. It has also made a splash in architecture from the Eiffel Tower to Shigeru Ban's work for the Aspen Art Museum (which consists of triangular lattice resin-infused paper that can support the roof despite its very low weight while providing a clear view of the semi-translucent roof above).
Lattices are also a large part of the visual appeal of such types of objects or architecture, opening up spaces with thin nodes or beams as opposed to solid blocks of material. Thus, they maximize transparency between the structural aspects of the various buildings, ceilings, furniture or towers. Landmarks like the Eiffel tower are mostly open air, yet still showcase a high strength-to-weight ratio.
They are also common in engineering items like heat exchangers or batteries, where transmission of energy needs to be optimal. The structure allows for covering a large surface area with minimal interfering parts, so it's also great for objects that need to be see-through or semi-permeable.
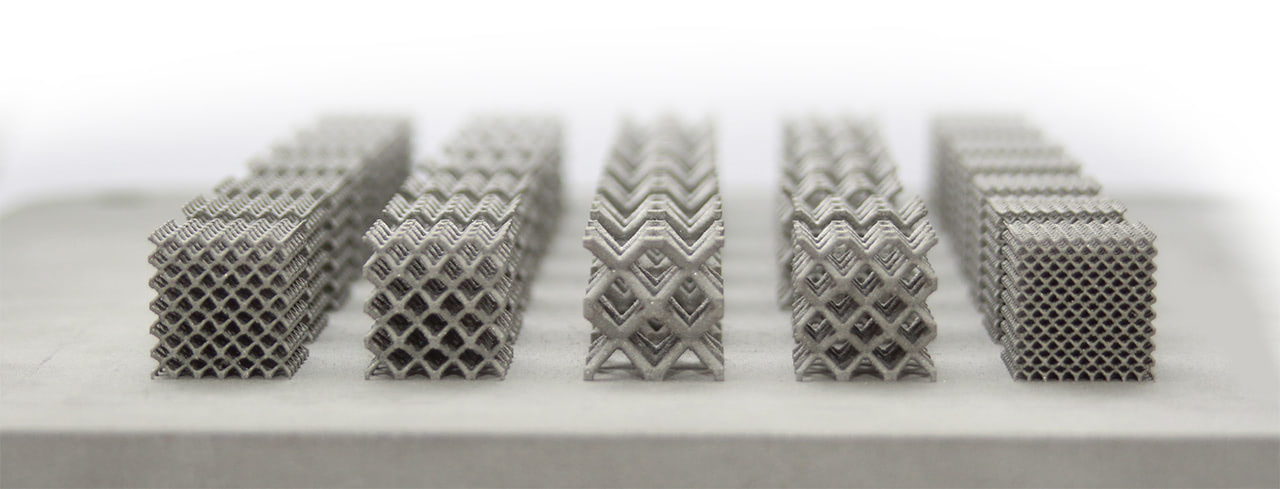
Why 3D Printed Lattices?
3D printing has given lattices new levels of accessibility. 3D printed lattice structures are far easier to produce due to the amount of control over internal geometry the technology offers. It's not just the hardware either. Topology optimization software, for example, have made it even easier to map out structures with precision.
Additionally, the layer-by-layer style of deposition allows greater control over hollow sections which are crucial for creating tiny nodes, beams and struts within the internal geometries of objects. Simply put, subtractive methods like CNC machining can not manage such parts by design.
Structural Advantages
The main reasons to 3D print lattices are the lightweight arrangements and high strength balance it can achieve. It also has major aesthetic benefits with its open spaces, complex nodes and a lot more design possibilities. However, there are also structural benefits that go beyond just strength weight or look.
Another advantage they possess is making use of the most amount of space with a low material usage. Lattices can expand on a design to improve its overall surface area without costing much in terms of materials as they stretch across nodes with a lot of open space in between.
By adjusting the thickness and position of the nodes, beams or struts, designers can integrate some novel features related to how the component interacts with forces and sound. Using lattices gives designers far more control over shock absorption, impact control and vibration/noise dampening. Similarly, designers can reduce impact stress or employ elements that act as a sacrificial features which protect the critical components of the object.
Design Considerations
There are a lot of little details that decide how well a lattice structure operates and what characteristics it has. Here are just a few:
Cell Structure & Size
There's a vast array of cell structures, which are individual building blocks in a lattice. Each cell represents a repeatable shape and can come in varying shapes and sizes. Usually, cell structures come in the standard shapes like cubes, stars, hexagons, diamonds and so on. However, many designers can mix and match these shapes to create specific material characteristics for a system. Not all structures are equal, so it's important to pick which shapes recur and in what order.
The size of the cell size and how densely the shapes repeat are key factors as well. Determining the cell size also relies on adjusting the thickness and length of its members and connecting nodes. High density of repetition simply means that there are more repeating shapes within one unit of area. High densities in a low amount of area will mean more complex tinier lattices. Larger cells are easily printable but can be stiffer overall. Similarly, smaller cells allow for more consistent system responses but are limited by feature sizes, i.e. have more homogenous responses but also have size-related limitations.
Material Selection
As with all 3D printing endeavors, your print is ultimately dependent on the right material and technology. These also influence the size and density that the lattice will have, as each material has its own rigidity, weight and other material properties to consider. Elastomeric or soft materials generally require a smaller and denser cell population to reduce sag during printing. Softer, less rigid materials also ordinary require thicker members and nodes. Alternatively, lattices printed with a more rigid material generally allow a greater design range with thinner members and larger cell sizes.
Cell Orientation
The angle at which cells are printed can alter a lattice structure's properties since it influences the amount and placement of supports required. However, one of the design advantages of a good lattice is that it can be self-supporting and stand on it's own. Certain designs also allow for easier printing at other angles. A large cubic truss, for example, printed directly on the build platform will find its horizontal members unsupported. However, if the structure is simply rotated 45 degrees, the members are now self-supporting.
Additive Manufacturing Design Examples

Vehicle Manufacturing
Various manufacturing industries have been leveraging the ability of 3D printers to lighten metallic structures. This is especially useful for automotive, aerospace and aviation, where vehicles have to be as light as possible to maintain speed and fuel efficiency. Sometimes this allows companies to reduce the weight of components by up to 70%.
The University of Nottingham focused on 3D printing complex metal lattice structures. In doing so, they reduced the weight of automobile components by decreasing their density. These new structural components would then allow the vehicle to weigh less overall, therefore becoming more fuel-efficient.
Similarly, the Nanyang Venture 8 was an electric car created by students and staff at the Nanyang Technological University. The car features over 150 3D printed parts, including the instrument cluster, various grills, door latches, but most crucially the outer shell and body consist of a honeycomb structure that enhances its strength.
Architecture
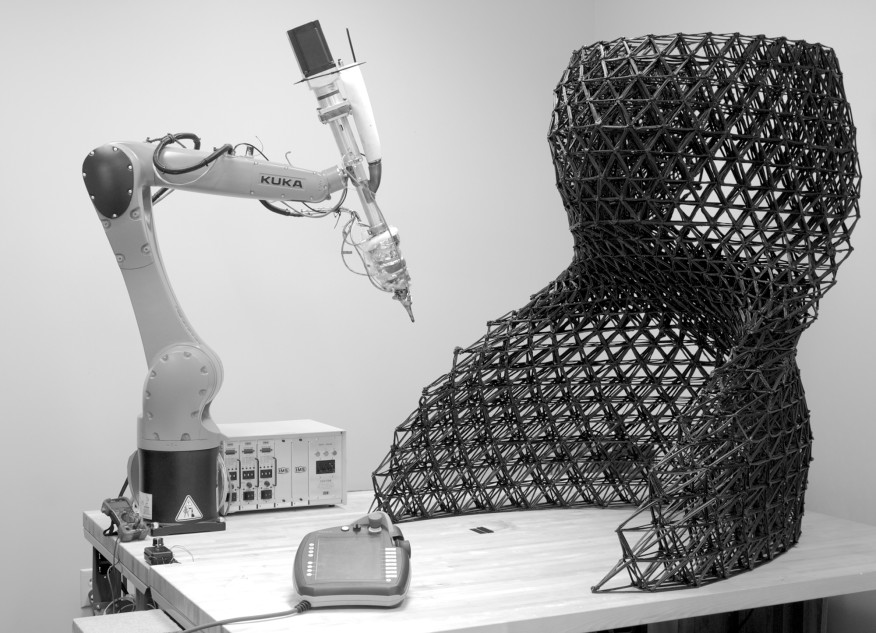
Various firms all over the world have been using 3D printed designs for all sorts of architecture and exhibits. At the Milan Design Week in 2019 fashion brand COS commissioned Conifera, a lattice-based installation using sustainable bioplastics. It was one of the largest 3D printed structures in the world, particularly among ones consisting of bioplastic. Part of this is the lattice structure that allowed it capture a much larger surface area, while using minimal materials.
Companies like Branch Technology have also been experimenting with lattice elements within architecture. They invented a 3D printed open-matrix lattice made from carbon-fiber reinforced ABS plastic that can serve as the core of a modular wall system that integrates common building materials like spray-foam insulation, spray-applied concrete, and cladding. It is light-weight and durable as well.
Sportswear

There are many examples of 3D printed lattices in sportswear, especially footwear midsoles. New Balance's work with the Triple Cell platform or Carbon and Addidas' Futurecraft 4D shoes. Both projects integrated a 3D printed lattice design directly into the structure of the shoes. The material could thus achieve a soft, bouncy quality while maintaining high strength and strong lattice structures. This makes the shoe design ideal for running shoes.
It's also being used for sports equipment manufacturing. Unstrung Customs would originally develop tennis handles with traditional manufacturing methods and fill them with polyfoam. Now, the company has switched to SLS, and ditched traditional molding. The weight-balance they achieved owes to the internal lattice structure of the 3D printed handle. Weight-balancing can be crucial for modern sports equipment, giving 3D printing an advantage over traditional manufacturing methods. 3D printing is very efficient at creating optimized internal structures for better aerodynamics, weight-balance and also to improve strength.
Similarly, football players are famously prone to on-field injury, particular head trauma. Carbon has tried to mitigate such injuries by 3D printing helmet liners for Riddell's smart helmets. They manufactured it using their "Diamond technology", creating lattice design pads out of resin, custom fitting the player's dimensions and position.
Research & Engineering
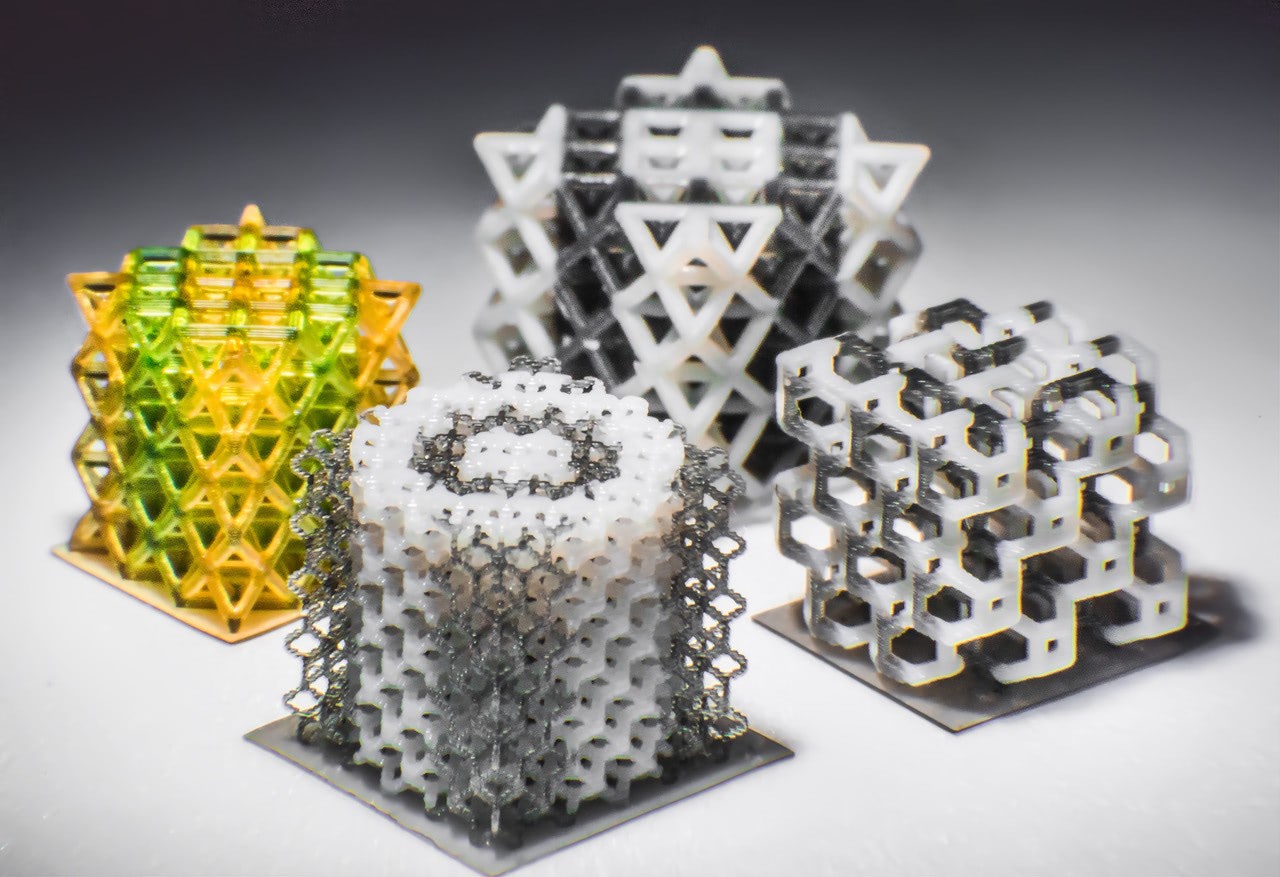
As mentioned previously, lattices have been used for a range of engineering purposes, most notable batteries. Lattice structures provide channels for effective transportation of electrolyte inside the volume of material, while for the cube electrode, most of the material will not be exposed to the electrolyte.
In normal batteries, 30-50% of the total electrode volume is unutilized. Our method overcomes this issue by using 3D printing where we create a microlattice electrode architecture that allows the efficient transport of lithium through the entire electrode, which also increases the battery charging rates." Rahul Panat, associate professor of mechanical engineering at Carnegie Mellon University.
Research into the materials and characteristics possibilities of 3D printing has been major advent for universities. Among these have been breakthroughs in how stiff and powerful internal geometries can be.
Research teams from ETH Zurich and MIT developed and fabricated material architectures that are equally strong in all three dimensions, and that are simultaneously extremely stiff. They were able to show that it's possible to determine mathematically in theory just how stiff materials with internal voids can become. A characteristic feature of the design is that the stiffness in the material's interior is achieved through plate-lattices rather than trusses.
ETH Zurich were also able to formulate the stiffest possible internal structure allowed by physical laws. Using intricate networks of trusses, girdles and arches, the researchers not only maximised stiffness, but also achieved this high strength printout using plastic. The print they designed also measures precisely equally in all 3 directions.
3d Print Hexagon Lattice Design Fusion 360
Source: https://3dprinting.com/tips-tricks/3d-printed-lattice-structures/
Posted by: baxteratudeas46.blogspot.com
0 Response to "3d Print Hexagon Lattice Design Fusion 360"
Post a Comment